8.2. Monitoring#
This section expands on practical and theoretical aspects of urban hydrological monitoring. It should be noted at this stage that not all the processes within the hydrological cycle can practically be monitored. Specifically, many of the fluxes in the hydrological cycle are not directly measured but can be inferred from measurements in the storages. Urban runoff is practically not measured, nor are the evaporative fluxes. However, other storages (unsaturated zone, precipitation, energy balance, in-sewer processes) will be expanded on here.
8.2.1. Spatial and temporal scale#
Before the details of the sensing can be discussed, the concept of monitoring networks needs to be explored. As mentioned in the introduction, not all fluxes are or can be quantified through monitoring. However, they can be inferred (through mass-balance based analyses) from a monitoring network, if the resolution of that network is high enough. The density of the monitoring network refers to the number of sensors/measurement locations per ha in the urban catchment.
A high density monitoring network is required in the urban area. This has two key reasons:
Due to the heterogeneity in urban fabric combined with the relative speed of the processes (fast run-off), there are strong local changes. In order to obtain a good understanding of the local complexities and dynamics, a dense monitoring network is required.
In principle, the aim of monitoring is to understand potential impacts on the population. Combining the heterogeneity with the presence of the local population means that it is considered more important to understand the processes at a smaller scale, as those processes can have a strong influence on the population.
Due to the speed of the urban processes, continuous monitoring is necessary. Continuous monitoring refers to the practices whereby information about the system is gathered continuously over a longer period of time. Other monitoring strategies, such as tracer experiments or grab samples—methods of system analyses where one has to take a measurement—are less ideal. Because urban hydrological processes are driven by rainfall and rainfall cannot be controlled, continuous monitoring through sensors allows the urban hydrological dynamics to be captured when they occur without complex planning. When we consider continuous monitoring, the frequency of information should ideally be less than a 5-minute resolution, in order to capture discharge peaks adequately. Although a higher frequency can be preferable from a system-understanding perspective, battery and data storage limitations can hinder this.
In practice, a large urban hydrological monitoring network with a high density is scarce. The data collected within the urban environment most typically serves either one of two purposes:
Operational use. Real-time decisions are required to make the urban hydrological system function as designed. For example, think of pumps that can be switched on and off. The data required for this is either directly linked to the local pumps, or sent to a SCADA at the WWTP or in any of the other locations in the city.
Regulatory use. Regulations govern the amount of water that is allowed to be discharged through CSOs. Monitoring of the processes can (and in the future will) be a regulatory requirement.
Monitoring networks that are set up with a sole purpose of better understanding (a part of) the hydrological cycle are not common. However, if a municipality or water board has noticed that there are negative consequences to their designed hydrological system, gaining insights through a comprehensive monitoring network can be a good starting point. For example, the city of Eindhoven, the Netherlands, in conjunction with the waterboard De Dommel, set up such a monitoring network through an integrated project (see Fig. 8.5). At a number of locations in the CSOs and at other places in the sewer network, the water level is monitored continuously. In addition, rain gauges were installed throughout the city to have greater spatial coverage of rainfall data. Several flow sensors were also installed, not only at the pumping stations but also at other key locations.
Fig. 8.5 Overview of the urban water monitoring network in Eindhoven, the Netherlands. The emphasis is on the monitoring of the CSOs, as the discharge from these structures has the largest negative consequence for the water quality in the area. (Own work)#
8.2.2. Process monitoring#
8.2.2.1. Hydro-meteorological monitoring#
8.2.2.2. In-sewer monitoring#
Sewer Level Monitoring
One of the key things that is monitored in real time is the water level within the drainage network. Monitoring within the sewer network is non-trivial. The presence of corrosive gases and solids (e.g. toilet paper, faecal matter, wet wipes) means that sensors touching the water directly will quickly degrade or give unreliable readings. In modern sewer monitoring networks, non-contact sensors are therefore preferred: ultra-sonic or radar sensors. Ultra-sonic sensors are mounted on the crest of a sewer pipe or underneath a manhole cover. To measure a water level, the sensor sends out an acoustic pulse and measures the time that the reflected pulse returns to the sensor. This time can be used to calculate the water level \(h\) through:
with:
Symbol |
Description |
Unit |
---|---|---|
\(h_{0}\) |
Length between the sensor and the invert of the pipe |
[L] |
\(\tau\) |
Measured time between the sent and received pulse |
[T] |
\(c_{air}\) |
Celerity of sound in air (usually around 343 m/s) |
[L/T] |
Measurements might be uncertain because \(c_{air}\) relates to the moisture content of the air, the temperature, and other physical disturbances between the sensor and the water level. Radar sensors, on the other hand, have less interference as they work with electromagnetic waves instead of acoustics. However, from a practical perspective, their comparatively high cost compared to more established acoustic sensors means that they are less used.
The water level is interesting to measure for a number of reasons. From a hydrological perspective, it can give an insight into the volume over a CSO. CSOs are weir structures, the flow over which is proportional to the head upstream of the weir. If we want to understand the flux from the sewer network to the surface water, the water level can (through a calibrated equation) provide sufficient information for this, whilst being relatively straightforward to monitor. Another key reason is that for a given section of the drainage network, there is a relation between the local water level and the amount of water in the upstream drainage network. This is the so-called H-V curve (head, volume) and takes a typical S-shape (see Fig. 8.6). The relation between the head and the upstream volume is derived through hydrodynamic modeling of the sewer network.
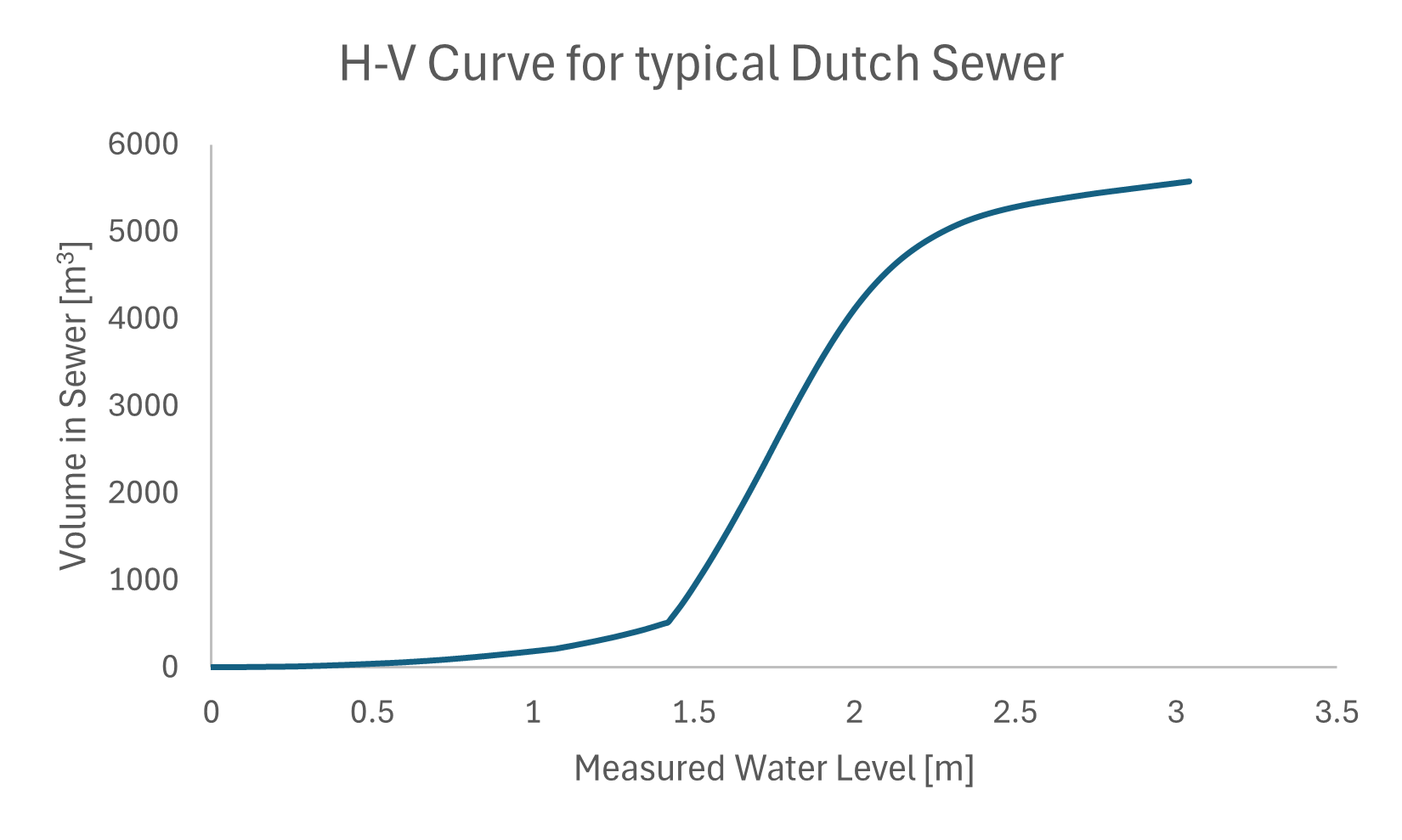
Fig. 8.6 Example of an H-V curve for a sewer district in the Netherlands. The x-axis shows the measurable water level at any location [\(L\)] and the corresponding upstream volume in the sewer network [\(L^3\)]. (Own work)#
One key benefit of monitoring water levels at a higher spatial resolution is that blockages and other issues within the sewer can be detected through the obtained data. Such failures, which are difficult to detect due to the buried nature of the infrastructure, can have a significant impact on the hydrological functioning of the system: if a system is partially blocked, the designed flow paths can be constrained, resulting in unplanned and uncontrolled discharges.
8.2.3. Flow Rate Measurement#
Measuring flow rates is notoriously difficult in-sewer. As previously highlighted in Section 7.2.1, the heterogeneity of flow velocities makes it nearly impossible to directly measure flow rates. However, in pressurized systems, this is more feasible using commercially available flow meters. The most common place to find flow measurements is therefore in the pressure main after a sewer pump. This measurement location is particularly useful as it provides insights into the performance of the pump, allowing operators to understand if the pump needs to be replaced or if there are other issues occurring that might not be obvious at first.
The most commonly applied sensor type is the electro-magnetic (EM) discharge sensor. These sensors use the principle that a conductive fluid moving through a magnetic field generates a voltage (see Fig. 8.7). The sensor output (a voltage \(E_{m}\)) is proportional to the cross-sectional velocity in the pressure main. As this pipe is fully filled (a property of pressure mains), this velocity multiplied by the cross-section of the pipe gives the flow rate. Commercially available sensors have been shown to have high precision and accuracy, with errors below 0.1%.
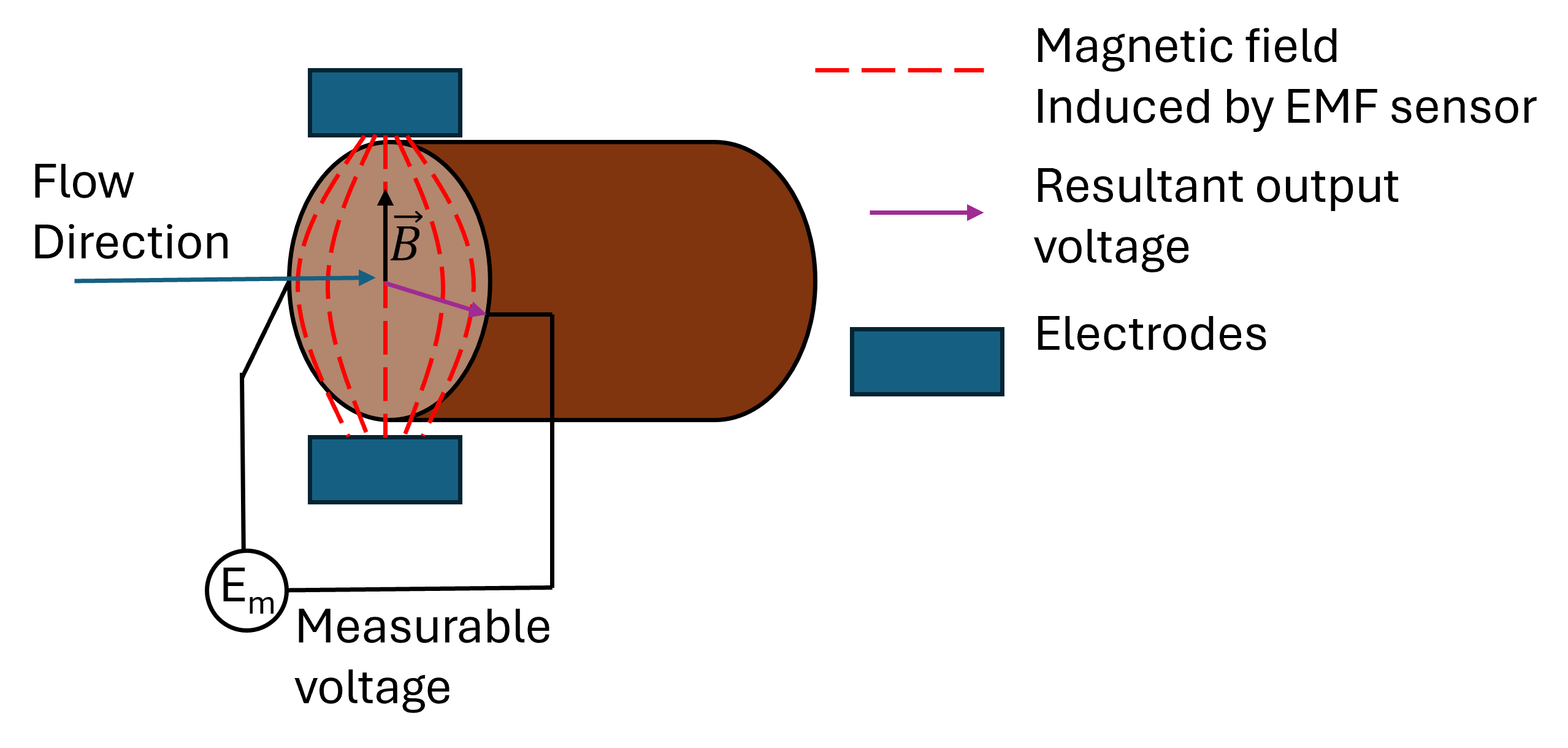
Fig. 8.7 Working principle of an electromagnetic flow meter. Two electrodes generate a magnetic field, perpendicular to the flow direction. This will create, following Faraday’s law, a perpendicular (right-hand rule) measurable voltage that is proportional to the velocity of the conductive fluid. (Own work)#
EM sensors can also be applied to measure the velocity profile in open-channel flow conditions. In this case, the EM is mounted on the invert elevation of the conduit or manhole where the monitoring is to be done and coupled with a water level sensor to combine both into a flow rate. Because of the location of the way the EM is mounted, the sensors output is related to a local velocity, not the mean or even representative flow velocity, leading to large uncertainties in the output. In addition, sensors that are necessarily mounted inside the stream of water can suffer from the corrosive sewer environment or be (partially) blocked by sedimentation of sewer solids.
8.2.3.1. Monitoring Blue-Green Infrastructure#
The designs of urban areas are increasingly relying on BGIs (Blue-Green Infrastructures) to store and infiltrate rainwater. The monitoring of this type of infrastructure presents new challenges that did not exist in sewer networks before. BGIs are not often connected, which means that the behavior of the systems cannot be inferred from the measurements in other parts of the system: they are, after all, their own individual piece of infrastructure. Additionally, the monitoring of processes above ground, although beneficial from a technical standpoint (as you don’t have to deal with corrosive gases), means that the monitoring system is more prone to vandalism.
In practice, BGIs are typically not monitored. The drivers for in-sewer monitoring (regulatory and operational) are not currently present for BGIs. Additionally, BGIs are above ground, which means that issues (blockages or flooding) can be monitored by keeping track of complaints from inhabitants. Additionally, if a municipality decides to go for a monitoring strategy for their BGIs, this is usually done through experimentation (infiltration tests) as opposed to continuous monitoring. During the infiltration tests, the BGI is isolated and a volume of water is put on top of it. Incrementally, the decrease in water level (due to infiltration) is monitored. This can be done with sensors or “simply” using a ruler. The infiltration rate of the BGI can then be calculated based on the derivative of the observed water level.
If the BGI has an underdrain, or any other type of outflow structure, it is ideally also monitored during the infiltration test. This will allow a better understanding of what part of the water infiltrates further into the ground and what part is discharged through this auxiliary structure. Although there are numerous ways to do this, the most common is by combining a water level measurement with a v-notch weir. This type of weir is particularly useful as relatively small variations in flow rate result in a significant upstream head difference (as the weir width gets progressively wider). The relationship between the measured upstream water level and the discharge is described by:
with:
Symbol |
Description |
Unit |
---|---|---|
\(Q\) |
Discharge |
\(\frac{L^3}{T}\) |
\(C_d\) |
Calibration constant |
[-] |
\(g\) |
Gravitational acceleration |
\(\frac{L}{T^{2}}\) |
\(\theta\) |
Angle of the v-notch |
[rad] |
A v-notch weir is assembled and calibrated off-site, ensuring that the calibration factor \(C_{d}\) is well-calibrated. The weir is then placed in front of the outflow pipe, ensuring that the outflow has to pass over the weir. The water level upstream of the weir is measured continuously (at a higher interval rate compared to standard monitoring (\(< 30\) s), allowing for the calculation of the total outflow flux. Knowing what was put into the system (the volume of water allowed to infiltrate) will allow a mass-balance approach to be taken to understand the hydrology of a BGI.